My Projects
Throughout my academic journey at Concordia University and during my high school years, I have had the privilege to engage in a diverse array of projects that span the breadth of mechanical engineering and beyond. This portfolio showcases the highlights of my work, reflecting my commitment to innovation, problem-solving, and technical excellence. I have also actively participated in various external events, further enriching my engineering expertise. Should you have any questions about my projects or wish to discuss them further, please feel free to reach out to me.
IPx9 & IPx6 Water Ingress Testing Chamber for Novabus
In my final year of university, my team and I overtook the challenge of creating a Water Ingress Testing Chamber for Novabus working closely with Novabus' testing engineers. The goal of the project was to create a testing chamber that can fit a 1'x1'x1' testing piece that can weigh up to 150 lbs. As IPx9 standards require pressurized water at 10MPa and 80 °C, we had to ensure a water-tight closure, both for proper testing and the safety of the operator. As it was a major project, we split the work where I mainly developed the turntable that will be carrying the test piece by selecting and designing bearings, pulleys, motors, and seals. Furthermore, I have aided my teammates with the overall structure design, plumbing layout, and manufacturing of the chamber itself.
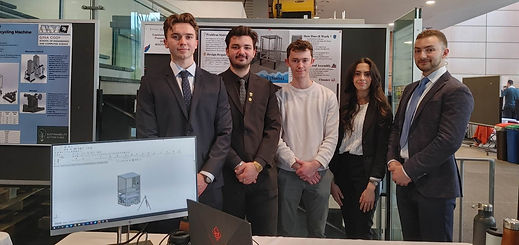
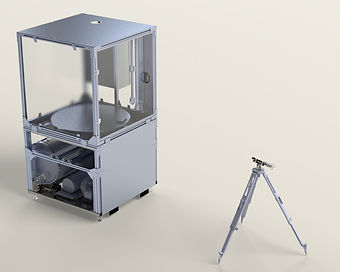

World's Smallest Automated Fiber Placement Head
During my time as a Research Assistant, I worked on designing and developing the World's Smallest Automated Fiber Placement Head. This need arises from the fact that all of the AFP solutions currently available are designed to be used on big parts such as plane wings, or car hoods. However, the need for carbon fiber-reinforced products that are considerably smaller is getting higher by the day. The images below show the final prototype we were able to achieve which employs a custom-made electronics/controller box, a completely re-designed head design using CATIA and Solidworks, and a proprietary software to run it. We have also developed simulation software using RoboDK and Python to simulate and test the narrowest angle our solution can reach which ended up being 79° degrees. I have learned countless vital skills such as how to use CATIA, the process of designing pneumatic-powered solutions, material properties of thermoset and thermoplastic carbon fibers, coding in Python and RoboDK, and custom PCB manufacturing.

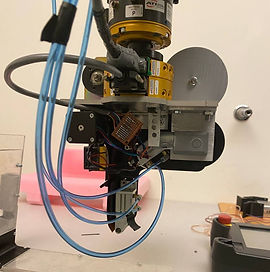
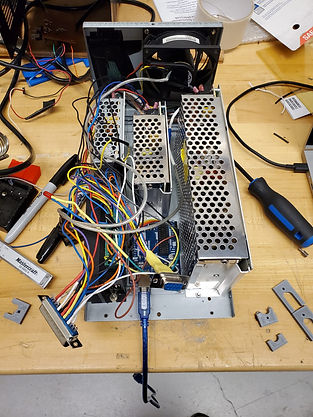
Honey Badger
As the team leader of the Concordia Machine Team for the Quebec Engineering Games, I led a team of 20 engineering students to create a solution for the challenge of the 2024 year. The solution is composed of two robots "The Honey" and "The Badger" names after our mascot The Honey Badger. The Badger (on the right) is capable of lifting itself and The Honey, and weighs around 15 kg. Furthermore, using its tracks, it can navigate on very harsh environments. On the other hand, The Honey can automatically pick up balls and use the launcher to send it to the badger for depositing. Both robots employ a custom made vacuum system in order to grab and transport the balls in the course. They both use Inverse Kinematics for their arms in order to ensure the driver is as comfortable as possible, and run on Raspberry Pi 4s coded with Python.
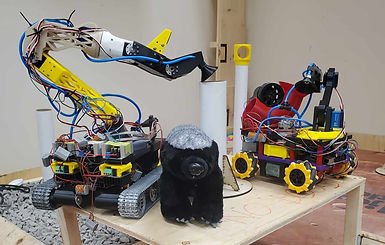
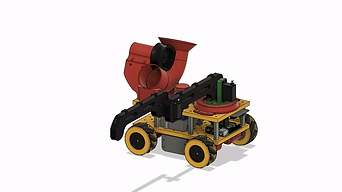

ConcoClean
At the Quebec Engineering Games, my team and I introduced an inventive dispenser-like machine named ConcoClean, which seamlessly combines common household items like water, vinegar, baking powder, and essential oils to produce custom cleaning products. This machine not only simplifies the production of cleaning agents but also tailors them to specific user needs, offering a versatile solution for home maintenance. We engineered and manufactured two prototypes, each integrated with a microcontroller, to demonstrate the concept. These prototypes played a pivotal role during the competition, effectively demonstrating the machine's functionality and potential to both the judges and the audience. The hands-on demonstrations proved essential in showcasing ConcoClean's practical utility and efficiency, earning us substantial recognition and support. Ultimately, our project secured 2nd place at the Quebec Engineering Games and 3rd place at the Quebec Engineering Competition, marking significant achievements at two of Quebec's premier engineering contests.

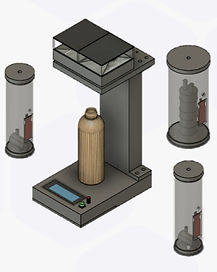

Object Identification with Image Recognition: An RC Car Battle
My team and I developed a sophisticated software capable of detecting moving objects and identifying various shades of colors through camera input. This software utilized advanced image recognition techniques, enabling it to precisely analyze and respond to visual data in real-time. Leveraging this technology, I applied the software to an innovative project: an automated RC car. This car was engineered to use the image recognition capabilities to detect and interact with objects within its vicinity. Specifically, it could identify and autonomously navigate toward other objects, hitting them with a laser as part of its functionality. This project was designed for a class at Concordia University where the RC car faced other robots. The main purpose of the robot was to detect the other RC car and hit it with a laser whilst avoiding being hit by other cars. This project not only showcased the practical applications of image recognition but also demonstrated the potential for integrating such technology into autonomous vehicles and robotics.



LQR for Inverted Pendulum on a Cart
My team and I coded and created a detailed control system for an inverted pendulum using MATLAB Simulink and Quanser equipment. This setup involved sophisticated controllers, including an LQR (Linear Quadratic Regulator) Controller designed to maintain the pendulum in an upright position by minimizing a cost function related to state variables and control efforts. Additionally, a Swing-Up Controller, developed using the Lagrangian Energy Method, was implemented to swing the pendulum from a hanging to an upright position. The integration of these controllers was visualized and tested through a comprehensive block diagram in MATLAB Simulink, which facilitated the understanding and simulation of the pendulum's dynamics. This project exemplified the practical application of advanced control theories and techniques in stabilizing an inherently unstable system, ensuring robust and efficient performance.

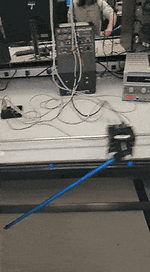
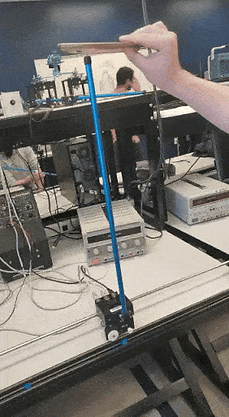
Semi-Automated Self Driving Car
I programmed a PID (Proportional-Integral-Derivative) controller to implement a cruise control function for a car, utilizing Arduino hardware and software technologies, including C++ and Register Level Programming. This controller was meticulously coded to manage the vehicle's speed automatically, adjusting it in real-time to maintain a constant velocity set by the user, which is a critical aspect of automotive automation.
Furthermore, to enhance the reliability and accuracy of this system, I modified and optimized various Hardware-In-the-Loop (HIL) simulators and ADC (Analog-to-Digital Converter) interrupts. These adjustments were crucial for ensuring that the system could correctly interpret sensor inputs and provide appropriate feedback for real-time adjustments. The adjustments also ensured that the HIL was perfectly simulating a real car's behavior. This involved extensive testing and calibration to fine-tune the interaction between the physical inputs from the vehicle's sensors and the software's response mechanisms, ensuring seamless integration and functional performance of the cruise control feature.


